HK-200WK Tank waveing automatic welding carriage
A welding carriage is a device used in welding operations.
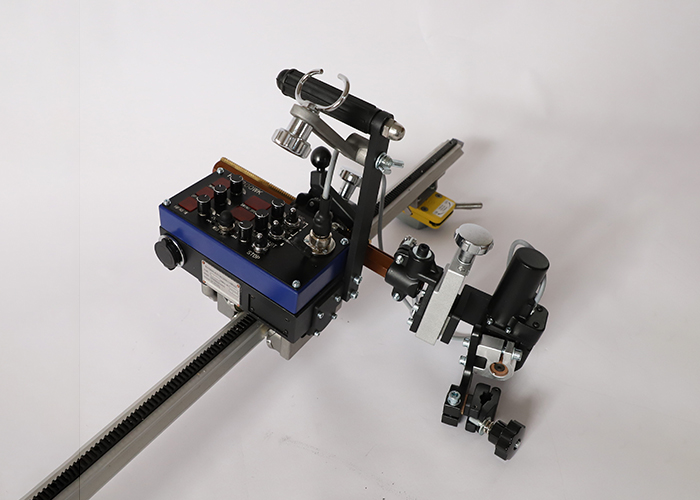
HK-200WK Tank waveing automatic welding carriage Detail Display
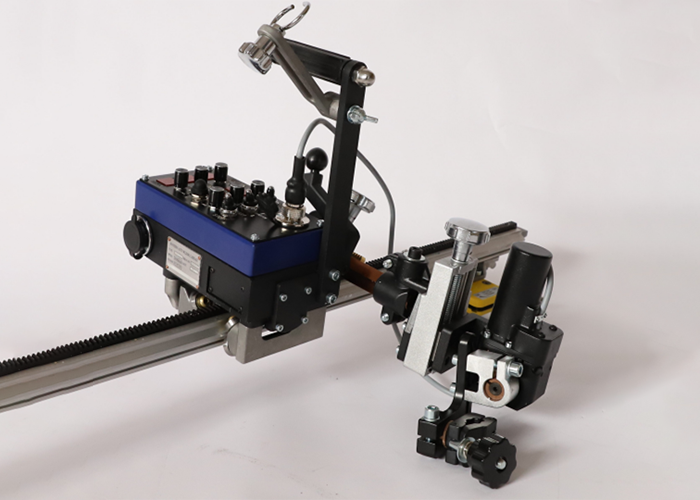
HK-200WK Tank waveing automatic welding carriage
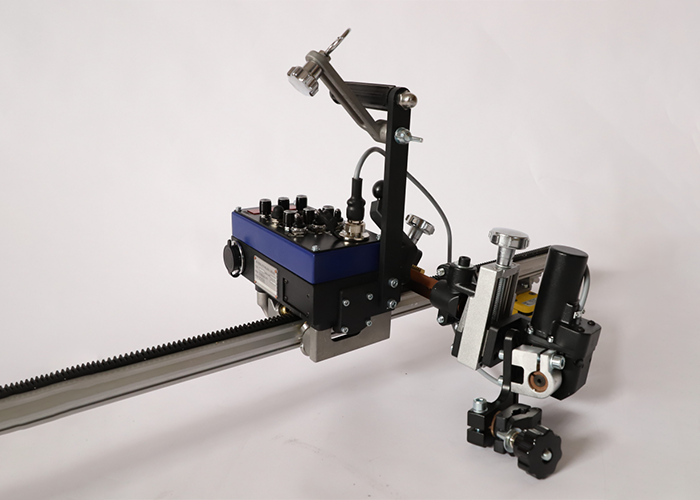
HK-200WK Tank waveing automatic welding carriage
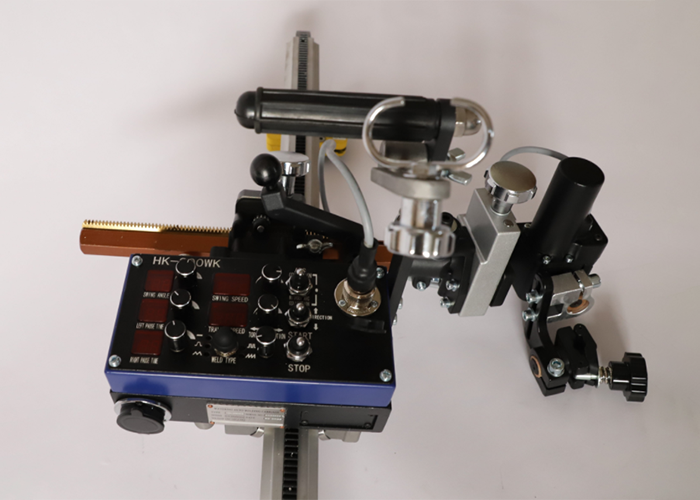
HK-200WK Tank waveing automatic welding carriage
Products Description
A welding carriage is a device used in welding operations. It is typically designed to hold and move the welding torch or electrode along a specific path. The carriage can be manually operated or automated. In automated welding, the carriage is programmed to follow a preset welding pattern, ensuring consistent and accurate welds. It often has features such as adjustable speed control, a stable base, and a mechanism for guiding the welding tool. Welding carriages are commonly used in industrial settings where large-scale welding projects are carried out, helping to improve productivity and weld quality.
KEY FEATURES
1.Docking, vertical, horizontal, and other multi-purpose automatic welding trolleys | 4.A manual clutch is installed in the driving part, facilitating the positioning of the machine on the track and its return to the welding starting point. |
2.The welding torch has a swing function. The optimal welding effect can be achieved by setting the swing speed, angle, center offset position, and left and right dwell time. |
5.The small track is convenient to move and is equipped with a clutch-type permanent magnet, which is convenient to use. |
3.The parameters of the speed and the swing head can be precisely set through digital display. |
6.It is widely applied in ships, bridges, locomotives, petrochemical industry, steel structure engineering, etc. |
Certification Marks:
Certified with CE, ISO 9001, ensuring compliance with international safety and quality requirements.
Main technical parameter
Model No. |
Supply Voltage |
L*W*H |
Up down |
Forward Backward |
Work Angle |
Processing Angle |
Method of driving |
speed |
weight |
HK-200WK |
AC220/50 |
540*240*300 |
60mm |
150mm |
45° |
+_15° |
Rack and pinion |
50-700 |
50 |
Advantages:
1.Improve welding quality: The welding carriagecan perform stable and uniform welding actions, ensuring consistency and aesthetics of the weld seam. It can precisely control welding parameters such as welding speed, arc voltage, and current, thereby improving welding quality.
2.Increase production efficiency: The welding carriage can automatically perform welding operations, reducing the time and labor required for manual welding. It can continuously work, increasing production efficiency, especially suitable for mass production.
3. Reduce labor intensity: Using a welding carriage, welders no longer need to hold the welding gun for a long time, reducing labor intensity. This helps reduce welders’ fatigue and the occurrence of occupational diseases.
4. Adapt to complex welding environments: The welding carriage can work in various complex welding environments, such as confined spaces and high-altitude operations. It can flexibly adjust the welding position and angle to meet different welding needs.
5. Improve safety: The welding carriage’s automated operation reduces the welders’ contact with the welding arc and high-temperature areas, reducing safety risks. At the same time, it can be equipped with safety devices such as guardrails and emergency stop buttons to further improve workplace safety.
HK-200WK Tank waveing automatic welding carriage FAQ
Q1: What types of welding carrages avaible? A: There are horizontal welding carriage, vertical welding carriage, gigid track welding carriage, flexible track welding carriage and so on. Q2: How to choose the right welding carriage? A:When choosing the right welding carriage, consider the following factors: 1.Welding Process – Determine the welding process you will be using. Different welding carriages are designed for specific processes such as MIG/MAG, TIG, or submerged arc welding. Make sure the carriage is compatible with your chosen welding method. 2.Workpiece Characteristics – Consider the size, shape, and material of the workpieces. For large and heavy workpieces, a carriage with a higher load capacity may be required. If you are welding on curved surfaces or irregular shapes, a flexible track carriage might be more suitable. – The material being welded can also influence the choice. Some carriages are better suited for certain materials, so ensure the carriage can handle the specific metal or alloy you are working with. 3.Welding Environment – If you are working in an outdoor or harsh environment, a rugged and weather-resistant welding carriage might be necessary. Pneumatic carriages can be a good choice in dusty or wet conditions. – For indoor use or areas with strict environmental requirements, an electric welding carriage with low noise and no pollution is a better option. 4.Precision and Quality Requirements – If high precision and quality welds are essential, look for a carriage with accurate positioning and control features. Rigid track carriages often provide better precision than flexible ones. – Consider the need for adjustable welding parameters and controls to ensure consistent weld quality. 5.Budget – Set a budget for your welding carriage purchase. There are a wide range of options available at different price points. Balance your requirements with your budget to find the best value for your money. By carefully considering these factors, you can choose a welding carriage that meets your specific welding needs and helps improve the efficiency and quality of your welding operations. Q3: How much does a welding carriage cost? A:The cost of a welding carriage can vary widely depending on several factors such as its type, features, quality, and brand. Here are some general price ranges: 1.Low-end models: Some basic or entry-level welding carriages can cost around $200 to $1,000. For example, simple magnetic or small portable welding carriages with limited functions and lower build quality might fall in this price range. 2.Mid-range models: These typically cost between $1,000 and $5,000. Mid-range welding carriages often have better build quality, more advanced features such as adjustable speed and welding parameters, and are suitable for a wider range of welding tasks. Models with flexible tracks or certain levels of automation might be in this category. 3.High-end models: Premium or high-performance welding carriages can cost $5,000 or more. These may be used in industrial settings that require high precision, complex welding operations, or have specific requirements for welding quality and productivity. Some advanced robotic welding carriages or those with sophisticated control systems and high-quality components can fall into this high-end price range. It’s important to note that prices can also vary depending on the supplier, region, and any additional accessories or features included with the welding carriage. When purchasing a welding carriage, it’s advisable to consider your specific welding needs and budget to find the most suitable option. Q4: Can I use seconde-hand welding carriages? A:You can use second-hand welding carriages, but there are several factors to consider: Advantages – Cost Savings: Second-hand welding carriages can be significantly cheaper than new ones, which can be beneficial if you’re on a tight budget. – Immediate Availability: You may be able to find a used carriage quickly, rather than waiting for a new one to be delivered or manufactured. Considerations – Condition: Thoroughly inspect the carriage for signs of wear and damage. Check the wheels, tracks, motor, electrical components, and welding torch holder. Look for cracks, bent parts, or excessive rust. – Functionality: Test the carriage if possible to ensure it operates smoothly and accurately. Check the speed control, direction control, and any adjustable features. Make sure the welding torch holder is secure and properly aligned. – Compatibility: Ensure that the used carriage is compatible with your welding equipment and processes. Check the voltage requirements, gas connections (if applicable), and any other specifications that may affect its use with your setup. – History and Maintenance: Try to find out the history of the carriage. Has it been properly maintained? Were there any major repairs or issues in the past? Ask for maintenance records if available. – Safety: Ensure that the used carriage meets all safety standards. Check for proper grounding, safety switches, and any other safety features. Make sure there are no electrical hazards or mechanical issues that could pose a risk to you or others. In conclusion, using a second-hand welding carriage can be a viable option if you carefully assess its condition, functionality, compatibility, and safety. However, it’s important to be cautious and make an informed decision to ensure that you get a reliable and useful piece of equipment. Q5: How to assemble a welding carriage? A:Assembling a welding carriage typically involves the following steps: 1.Gather all Components – Check that you have all the parts of the welding carriage, including the frame, wheels or tracks, motor (if applicable), welding torch holder, electrical components, and any accessories or fasteners. 2.Prepare the Workspace – Clear a clean and flat work area where you can assemble the carriage without obstructions. Have your tools handy, such as wrenches, screwdrivers, pliers, and any specialized tools required for the specific model. 3.Frame Assembly – Start by assembling the frame of the carriage. Follow the manufacturer’s instructions to connect the various pieces of the frame using bolts, screws, or welding if necessary. Ensure that the frame is square and stable. 4.Install Wheels or Tracks – Depending on the type of carriage, install the wheels or tracks. Make sure they are properly aligned and secured. Check for smooth rotation and proper fit. 5.Mount the Motor (if applicable) – If the welding carriage has a motor for movement, mount it securely to the frame. Connect the motor to the power source and any control systems according to the instructions. Test the motor to ensure it operates correctly. 6.Install the Welding Torch Holder – Attach the welding torch holder to the carriage. Adjust it to the desired height and angle, and make sure it is firmly fixed in place. Ensure that the torch can be easily inserted and removed. 7.Electrical Connections – If there are electrical components, such as switches, wires, and controllers, make the necessary electrical connections. Follow the wiring diagrams provided and ensure proper grounding for safety. Test the electrical functions to make sure everything is working as expected. 8.Final Checks and Adjustments – Once the assembly is complete, perform a final inspection of the welding carriage. Check for any loose parts, misalignments, or potential safety hazards. Make any necessary adjustments to ensure smooth operation and proper functionality. It’s important to note that the specific assembly steps may vary depending on the type and model of the welding carriage. Always refer to the manufacturer’s instructions for detailed and accurate assembly procedures. If you are unsure about any step, it may be helpful to consult an experienced welder or seek professional assistance. Q6:How do I ensure the safety of using a second-hand welding carriage? A:To ensure the safety of using a second-hand welding carriage, consider the following steps: Inspection – Thoroughly inspect the carriage for any visible damage. Check for cracks, bent parts, worn-out wheels or tracks, and loose connections. Look closely at the frame, motor housing, and welding torch holder. – Examine the electrical components. Check for frayed wires, damaged insulation, and proper grounding. Make sure all switches and controls are in good working condition. Functionality Test – If possible, test the carriage’s functionality before using it. Run it through its full range of motion to ensure smooth movement and proper operation of the motor (if applicable). Check the speed control and direction controls. – Test the welding torch holder to make sure it securely holds the torch and can be adjusted as needed. Maintenance and Repair – Perform any necessary maintenance or repair before using the carriage. Replace worn-out parts such as wheels, belts, or brushes. Tighten loose bolts and nuts. – If there are any electrical issues, consult a qualified electrician to ensure safe operation. Safety Features – Check for safety features such as emergency stop buttons, overload protection, and proper shielding. Make sure these features are in working order. – Use appropriate personal protective equipment (PPE) when operating the welding carriage, including welding helmets, gloves, and protective clothing. Research and Documentation – Try to obtain as much information as possible about the history of the carriage. Look for maintenance records, user manuals, or any safety certifications. – Research the make and model of the carriage to learn about any common safety issues or recalls. By following these steps, you can increase the safety of using a second-hand welding carriage and reduce the risk of accidents or injuries.
- +8618858825816
- [email protected]
- No.39, Sitong Road, Zhuangquan Country, Tianhe Street, Wenzhou Economic And Technological Development Zone, Wenzhou City, Zhejiang Province, China
HK-200WK Tank waveing automatic welding carriage More About Reto
Application Areas
CO2 welding automatic trolley is widely used in ship, bridge, locomotive, steel structure, petrochemical industry and other industries. It is suitable for welding various welding structures, such as: welding of reinforcing ribs, ribs, cross parts, welding of box girders, etc. Its main advantages are reducing labor intensity, improving working environment and improving work efficiency, which is 1.5 times higher than that of manual welding, avoiding poor quality of welds caused by human factors. Generally, poor rate of manual operation is about 20%, while automatic welding trolley does not produce poor rate of welding, so its comprehensive benefit is nearly 200% higher than that of manual welding.High degree of automation to ensure the stability of welding quality.