YJJ-A-200 Suction Self-controlled Flux Drying Machine
Suction self-controlled flux drying machine is a device that uses suction and self-control technology to achieve flux drying.
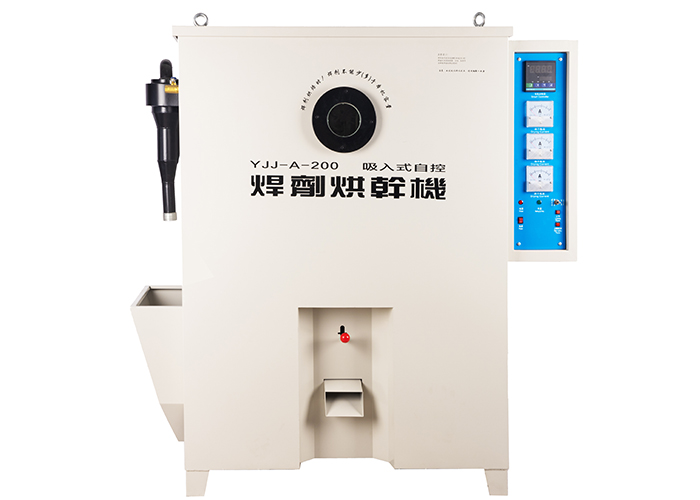
YJJ-A-200 Suction Self-controlled Flux Drying Machine Detail Display
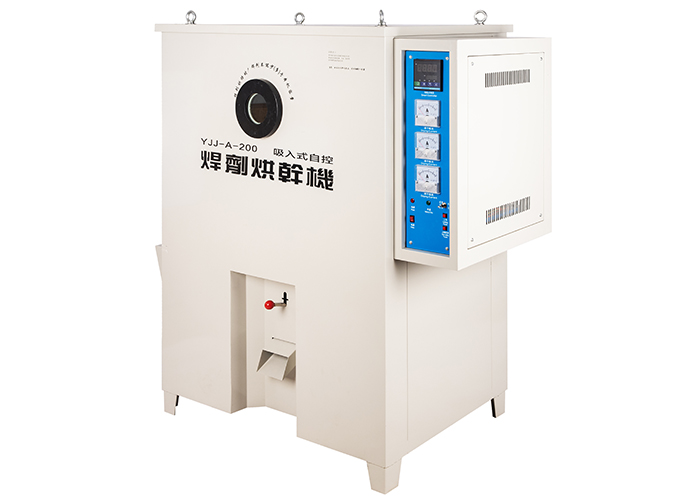
YJJ-A-200 Suction Self-controlled Flux Drying Machine
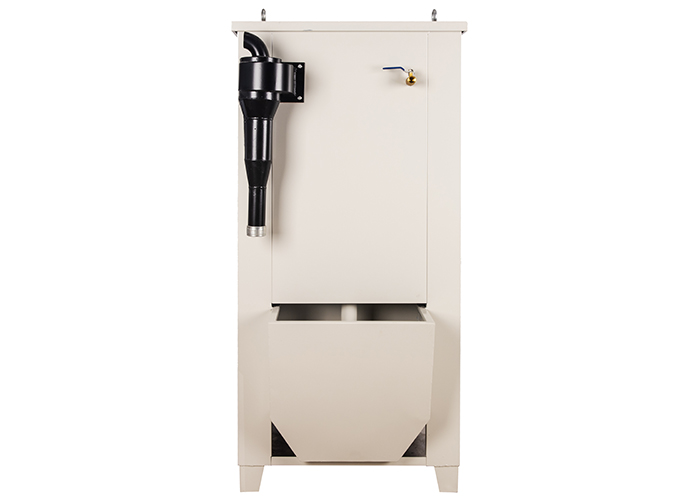
YJJ-A-200 Suction Self-controlled Flux Drying Machine
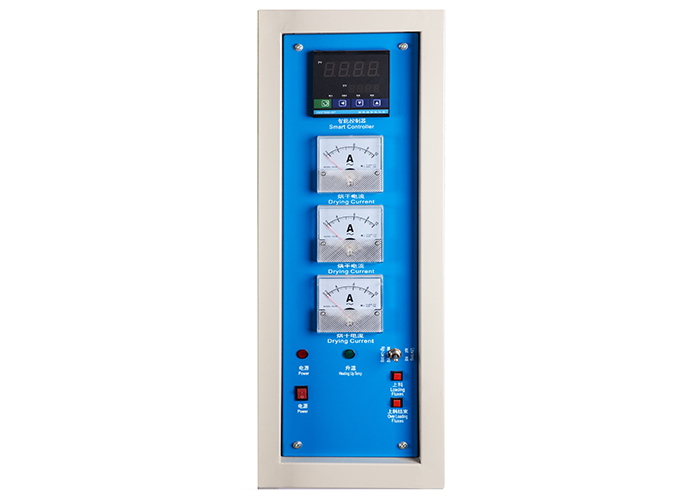
YJJ-A-200 Suction Self-controlled Flux Drying Machine
Products Description
Suction self-controlled flux drying machine is a device that uses suction and self-control technology to achieve flux drying. It can effectively remove moisture and ensure the drying quality of the flux. This kind of drying machine is usually equipped with advanced control systems to adjust parameters such as temperature and air flow according to different drying requirements, providing stable and efficient drying performance.
Key Features
1.This dryer is provided with automatic suctionand dust wiper mechanism. | 3.Stainless steel heating tube |
2.Drying tank is made of stainless steel. | 4.Uniformly heated to achieve optimaldrying effect |
Certification Marks:
Certified with CE, ISO 9001, ensuring compliance with international safety and quality requirements.
Product Information
1.suction silo | 6.Ammeter |
2.peep mirror | 7.Voltmeter |
3.Discharge handle | 8.High and lowtemperature switch |
4.outlet | 9.Dust Collector |
5.Intelligent digitalinstrumentation | 10.Exhaust valve |
Parameter
MODEL NO. | YJJ-A-100 | YJJ-A-200 | YJJ-A-300 | YJJ-A-500 |
Flux Capacity | 100L | 200L | 300L | 500L |
Max.Working Temperature | 450℃ | 450℃ | 450℃ | 450℃ |
Voltage | 380V-415V | 380V-415V | 380V-415V | 380V-415V |
Frequency | 50Hz | 50Hz | 50Hz | 50Hz |
Electric Power | 3.6kw | 3.6kw | 7.2kw | 10.8kw |
Feeding Machine Power | 1.5kw | 1.5kw | 1.5kw | 1.5kw |
Suction Speed | 180kg/h | |||
Temperature Raising Speed | 200℃/h | |||
Adjustable Heating Time | 0-10h | |||
Dimension
L×W×H(mm) |
1310x1355x650 | 1320×700×1700 | 1510x1440x700 | 1580x1730x800 |
Weight | 100kg | 150kg | 180kg | 220kg |
Moisture determination of dried flux | 0.05%≤ |
Productelectrical Components Table And Electrical Schemati
Serial number | Name | Model | Quantity | Remarks | Code |
1 | Universal input double four | MT—101(0~500℃) | 1 | Choose one | XMT |
2 | Intelligent quantity adjuster | TDA—8001(0~500℃) | 1 | TDA | |
3 | Thermocouple | K/200mm | 1 | Nickel – nickel silicon | K |
4 | AC ammeter | 44L1—A | 1 | A | |
5 | Heater | 1.0KW/pc | 6 | 100 Type | R |
1.2KW/pc | 6 | 200 Type | |||
1.6KW/2pcs 2.4KW/6pcs | 8 | 300 Type | |||
4.0KW/pc | 12 | 500 Type | |||
6 | AC contactor | CJ10—20A/220V | 2 | 20A | C |
7 | Digital display time relay | JS11J/220V | 1 | 1min~9h 59min | JS |
8 | power switch button | 1 | K2 | ||
111C/88 | 1 | K3 | |||
PB-307A | 2 | K1 K4 | |||
9 | Indicator light | XD-220V | 4 | XD | |
10 | Screw fuse | RL1-15 | 1 | With the core 2A | 2RD |
11 | Screw fuse | RL1-60 | 3 | With the core 3A | 1RD |
12 | Feeding fan | 1.5KW 380V | 1 | D | |
13 | Relay | 522/AC220V | 1 | J | |
14 | Thermal allergy relays | TGR36-20 | 1 | JR |
Performance:
1.The use of dryer inside the feeder, can automatically from the hopper inhalation into the dryer dryer in the dryer, without artificial loading。
2.Dryer tube tubular heating tube layout is reasonable, uniform temperature, liner and electric heating tube are made of stainless steel, eliminating the rust on the pollution of the flux。
3.Electric heating tube long life, for example: YJJ-A-500 flux dryer within the U-type heating tube a total of 12, each power 4KW。
4.Temperature automatic control, can be arbitrarily adjusted baking temperature. When the temperature reaches the intended requirement, it can be automatically thermostat, controlled by the digital time relay at constant temperature. To set the time to constant temperature, that is automatically cut off the power。
5.Equipped with peephole, can be free to observe the situation inside the dryer。
6.Easy to take material, as long as the press out of the handle, after drying the flux from the bottom out of the mouth, off the handle that is closed。
7.Equipped with dust removal device, in the suction process can simultaneously remove the dust in the dust collected in the dust collector, to ensure the quality of flux welding。
YJJ-A-200 Suction Self-controlled Flux Drying Machine FAQ
Q1.What are stick electrodes and what is shielded metal arc welding (SMAW)? SMAW (Shielded Metal Arc Welding) is a manual arc welding process that is often called stick welding. It is one of the most popular welding processes used today. Its popularity is due to the versatility of the process and the simplicity and low cost of the equipment and operation. SMAW is commonly used with such materials as mild steel, cast iron, and stainless steel. The process requires a consumable electrode that is coated in flux (stick rod) to lay the weld, and an electric current is used to create an electric arc between the electrode and the metals that are being welded together. The electric current may be either an alternating current or a direct current from a welding power supply. While the weld is being laid, the electrode’s flux coating disintegrates. This produces vapors that provide a shielding gas and a layer of slag. Both the gas and slag protect the weld pool from atmospheric contamination. The flux also serves to add scavengers, deoxidizers, and alloying elements to the weld metal. Q2.What are the proper storage and rebaking guidelines for stick rods? For specific storage and rebake temperature guidelines, we recommend contacting the welding consumable manufacturer directly. It is also important to check with local welding codes and/or ask a welding inspector to provide some information. Welding standards change frequently, and each manufacturer often provides a different recommendation regarding welding electrode storage. Check the packaging and also manufacturer websites for information. Keen offers a wide range of products to handle almost any welding consumable storage requirement. Q3.What are the key differences between welding rod holding ovens and welding rod rebake ovens? Keen rod ovens are specifically designed according to the temperature range of the process, and the amount of electrodes to be stored. The standard holding ovens are designed to accommodate a maximum temperature of 300℃and the rebake ovens are designed to reach 500℃. The higher temperature ovens have larger wall thicknesses to accommodate more insulation, explosion proof latches and digital programmable temperature controllers. The large, floor-positioned holding ovens feature basic digital temperature control, and the bench and portable ovens have analog temperature control or constant input without thermostatic control. Q4.Can I use a Keen portable holding oven for long term storage? Portable welding electrode ovens are designed primarily for short-term holding, not long-term holding. Portable units are commonly used by individual welders in the field to keep electrodes dry at the welding station. Typically, welders are provided electrodes that are stored in a larger, long-term holding oven at the tool crib. They load up their portable for a day’s work, and any that are left at the end of the day are returned to the crib for rebaking or long term storage. The portable is shut off until the next time it is used in the field. Q5.Are the large ovens used only for long term storage? Yes. Electrode holding ovens from 200 lbs capacity and up are designed to be run 24 hours/day, 7 days/week. The idea is to keep all unpackaged electrodes at elevated temperatures all the time to preserve the integrity of the electrode and to ensure optimal welds. Q6.How can I determine the amp draw for a particular rod oven model? Use this formula: Watts / Voltage = Amps Q7.Are there any commonly known welding rod storage methods that are inadequate? One welding rod storage myth perpetuated by some in the industry is that an old refrigerator equipped with a light bulb will sufficiently heat the covering on low-hydrogen electrodes to the consumable manufacturer recommended storage temperature range of 225-300F. Most light bulbs do not provide sufficient heat to bring the electrodes up to the proper temperature to stave off moisture contamination in the covering. Another myth that we have come across over the years is that storing welding electrodes in a freezer will keep the rods dry. This of course is a myth because as soon as the rods are removed from the freezer they will be a magnet for any atmospheric moisture that exists in the air and produce condensation on the coating. It is always best to review instructions on the manufacturer’s packaging, and to consult the manufacturer for guidelines of if you have any questions pertaining to proper storage. Please note that not everyone is informed about welding rod storage, even in customer service departments at major manufacturers. It is best to speak with an experienced welder or inspector that knows AWS SMAW specifications and proper industry-approved storage guidelines. Q8.What are common storage and handling mistakes that can lead to damaged welding rods? Welding electrodes are manufactured to be within acceptable moisture limits consistent with the type of covering and strength of the weld metal to be used with the electrode. They are then packaged in a container which has been designed to provide the degree of moisture protection considered necessary by the industry for the type of covering involved. Some common handling mistakes of welding rods are: Exposing to atmospheric moisture beyond the consumable manufacturer’s suggested time limits Storing rods in opened factory packaging Opening the container from the wrong end Tossing the rods around which can crack the low hydrogen coating on the welding rods thus rendering them useless Exposing to abrupt temperature fluctuations, particularly from cold to warm areas – condensation may be drawn to the coating Exposure to grease or dirt which also contains moisture Q9.What issues can potentially result during welding from improperly stored welding rods? Poor arc direction, excess spatter, poor shielding, lack of penetration and porosity are common results that occur when welding rod coatings have been contaminated by moisture. Another common occurrence is “fingernailing” which is a term used to describe uneven burn-off on one side of the welding rod. This is often due to moisture contamination in one area of the electrode causing it to burn off more slowly than other areas. Q10.What terms should I know that are related to poor storage of welding consumables? Porosity: formed by entrapment of discrete pockets of gas in the solidifying weld pool. The gas can be formed in a variety of ways: poor gas shielding, surface contaminants such as moisture, grease, rust. Porosity can also result from insufficient deoxidants in the parent metal, electrode of filler wire. Wormholes: A severe form of porosity caused by heavy contamination of the weld pool as a result of surface contamination or welding with damp electrodes. Under radiograph, they appear as elongated pores and are indicative or a large amount of gas that has formed in the weld which is trapped by the solidifying weld metal. Hydrogen: Contributes to cracking in the solidified weld. In combination with high tensile stresses and sensitive steels, hydrogen can cause cold cracking several hours or days after the weld is complete. For structural welding using high strength steels, consumables that give low hydrogen levels are often used. These types of consumables are prone to moisture pick-up and must be stored at elevated temperatures. Q11.How can I tell if the coating on my low-hydrogen welding rods has been compromised? Visually inspect the rod coating to determine if the color has changed during storage. Any discolored welding rods should be discarded or your supplier should be contacted. Also visually inspect for physical damage to the coating that may have occurred during handling. Any sections of the rod coating that may have been damaged will render the rod useless and it should therefore be discarded. Q12.How can I find recommended storage guidelines from the manufacture of my consumable? Check the consumable packaging for information, your local supplier and/or the manufacturer of the consumable you purchased. Please note that not everyone is informed about proper welding rod storage, even in customer service departments at major manufacturers. It is best to speak with an experienced welder or inspector that knows AWS SMAW specifications and proper industry-approved storage guidelines. Q13.How do storage methods differ for low hydrogen rods, stainless steel rods, cellulosic rods and non-low hydrogen rods? Proper storage procedures should be followed for all types of welding electrodes. Please consult the consumable manufacturer for specific instructions. It is generally accepted that the same storing and rebaking procedures for low-hydrogen welding rods also apply to stainless steel welding rods. Cellulosic electrodes should not be stored in an oven because moisture exposure does not have a detrimental effect on performance. If non-low-hydrogen rods have been exposed to moisture, they can be heated in a rod oven at low temperatures only (100-120°F). Q14.Can I store different types of welding electrodes simultaneously in a rod oven? This can present some problems, and the consumable manufacturer must always be contacted before storing multiple types of electrodes together in a single rod oven. Welding electrodes are manufactured to have a specific range of moisture content. For example, low-hydrogen rods have a moisture content of approximately 0.1 – 0.4 percent. Cellulosic rods on the other hand have a moisture content of 4 to 6 percent. If these two types of electrodes are stored in the same oven, the lower moisture content low-hydrogen rods will absorb moisture from the higher moisture content cellulosic rods. It is important to note that cellulosic rods are not to be stored long term in a rod oven, and are only heated at low temperatures (100-120°F) if they have been exposed to humid air for an extended period of time.
- +8618858825816
- [email protected]
- No.39, Sitong Road, Zhuangquan Country, Tianhe Street, Wenzhou Economic And Technological Development Zone, Wenzhou City, Zhejiang Province, China